Thread rolling is a fastener production method that involves impressing screw or bolt threads into the raw stock rather than cutting them. This process makes use of a hardened-steel tool bit formed in the shape of the relevant thread. The raw, unformed stock is rotated at a controlled rate while the tool bit is pressed against it under high pressure, causing the form of the screw thread to be impressed upon the stock surface. The tool bit is constantly kept under pressure and advanced towards the stock until the threads are formed to their full depth. Thread rolling is less costly as a production process than thread cutting, and yields stronger, safer end products.
Bolts and screws are amongst the most commonly used fasteners, with huge quantities produced annually across the world. These fasteners are generally mass produced from raw metal stock, which is pre-formed prior to the introduction of the threads. There are two basic methods used to form the threads, namely thread cutting and thread rolling. Thread cutting utilizes a cutting die that is advanced up the length of the revolving blank stock physically cutting away the metal surface to form the threads. Although effective, this method is time-consuming while generating heat that may weaken the fastener.
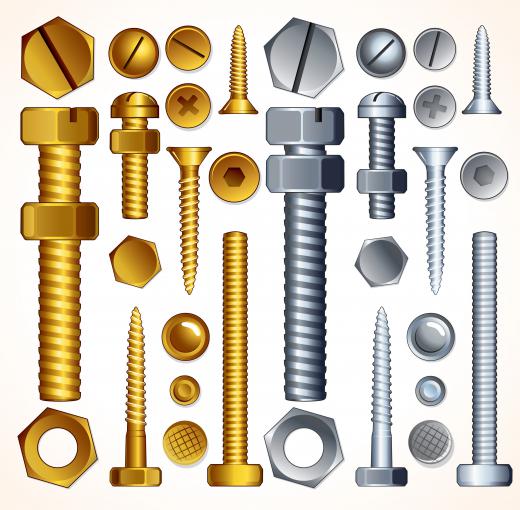
The second method, thread rolling, is a superior process in several senses. In this process, a hardened tool bit is used to press the threads into the surface of the stock. The tool bit is formed in the shape of the threads and is forced, under great pressure, against the stock, which rotates at a controlled rate. Increasing pressure causes the tool bit to gradually impress its shape on the softer metal stock. As the threads begin to form, the tool bit is advanced towards the stock maintaining the pressure exerted against it. This causes the impressed threads to deepen until they have reached their full depth.
The thread rolling process holds several benefits over thread cutting. The machinery required is simpler, the process requires less steps with resultant increases in productivity, and the tool bits have a longer life making for a good overall cost and yield advantage. The process of thread cutting also generates high temperatures that tend to weaken the metal stock. Thread rolling is a cold working process and produces end products that are inherently stronger. Rolling also generates no chips, or swarf, which produces a cleaner environment and reduces the danger of injuries caused by sharp, freshly-cut threads.