Thin film deposition is a technique used in industry to apply a thin coating to a particular design part made of a target material and to infuse its surface with certain properties. Thin film coatings are applied to change the optical properties of glass, the corrosive properties of metals and the electrical properties of semiconductors. Several deposition techniques are employed, usually to add atoms or molecules, one layer at a time, to a vast array of materials that lack essential surface properties that thin coatings provide. Any design for which a coating of minimum volume and weight is required can benefit from thin film deposition that exposes a target material to an energized environment of liquid, gas or plasma.
The first crude metal coatings were used in the first millennium to improve the reflective properties of glass for mirrors. The 1600s saw the development of more refined coating techniques by Venetian glassmakers. Not until the 1800s did precision methods of applying thin coatings, such as electroplating and vacuum deposition, exist.
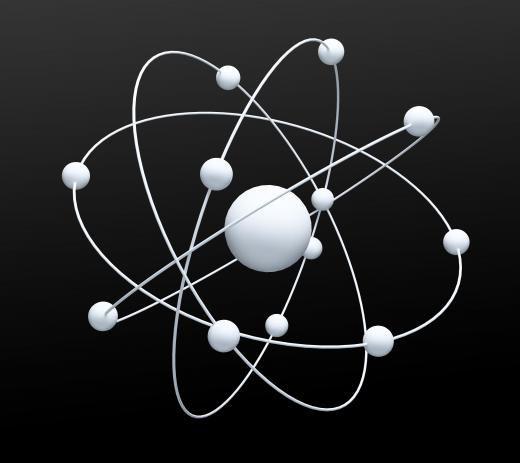
Electroplating is a form of chemical deposition in which the part to be coated is attached to an electrode and submerged in a conductive solution of metal ions. As a current is run through the solution, the ions are drawn to a part’s surface to slowly create a thin layer of metal. Semisolid solutions called sol-gels are another means of chemical deposition of thin films. As long as the coating particles are sufficiently small, they will remain in suspension in the gel long enough to organize into layers and provide an even coating when the liquid fraction is removed in a drying phase.
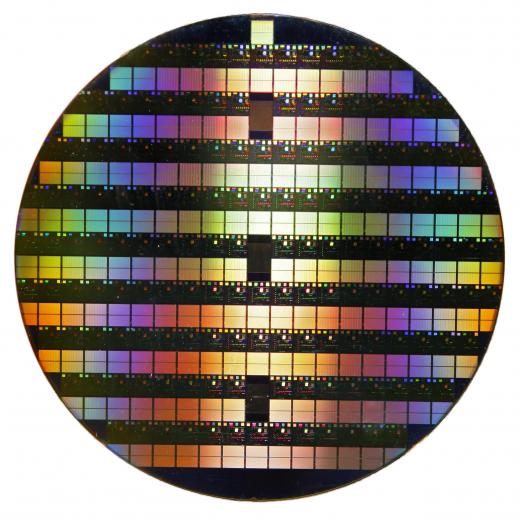
Vapor deposition is a technique for creating thin film deposition in which a part is coated in an energized gas or plasma, usually in a partial vacuum. In the vacuum chamber, atoms and molecules spread out evenly and create a coating of consistent purity and thickness. By contrast, with chemical vapor deposition, the part is placed in a reaction chamber occupied by the coating in gaseous form. The gas reacts with the target material to create the desired coating thickness. In plasma deposition, the coating gas is superheated into an ionic form that then reacts with the atomic surface of the part, typically at elevated pressures.
In sputter deposition, a source of pure coating material in solid form is energized by heat or electron bombardment. Some of the atoms of the solid source come loose and are suspended evenly around the part’s surface in an inert gas, such as argon. This type of thin film deposition is useful in viewing fine features on small parts that are sputter-coated in gold and observed through an electron microscope. In coating the part for later study, gold atoms are dislodged from a solid source above the part and fall onto its surface through a chamber filled with argon gas.
The applications of thin film deposition are diverse and have been expanding. Optical coatings on lenses and plate glass can improve the properties of transmission, refraction and reflection, producing ultraviolet (UV) filters in prescription glasses and anti-reflective glass for framed photos. The semiconductor industry uses thin coatings to provide improved conductance or insulation for materials such as silicon wafers. Ceramic thin films are anti-corrosive, hard and insulating; though brittle at low temperatures, they have been used successfully in sensors, integrated circuitry and more complex designs. Thin films can be deposited to form ultra small “intelligent” structures such as batteries, solar cells, drug delivery systems and even quantum computers.