Thermoforming is a manufacturing process which involves heating a material until it is pliable, stretching it over a mold, and then cooling it so it retains the desired shape. A variety of materials, including bone and shells, have been processed in this manner for centuries, though thermoforming is now primarily used for shaping plastic sheets or films. Examples of thermoformed products include blister packing for pills and individual food servings, plastic trays, and even plastic pallets.
The most common method of thermoforming is straight vacuum forming. This process involves heating a sheet of plastic to its sag point and then lowering it into a recessed mold. The air is removed by vacuum, plastering the sheet against the walls of the mold. The plastic is cooled and then trimmed and removed if necessary. Equipment required for straight vacuum forming is generally much cheaper than the equipment required for pressure or mechanical processing.
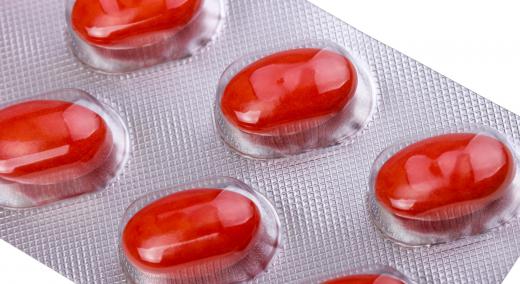
A more expensive thermoforming method used for parts which require exact detailing is matched mold forming. In this process, a sheet of plastic is stretched between two matching, heated molds. The molds are pressed together and air bubbles removed by vacuum through holes in the molds.
When plastic sheets need to be molded into deep shapes requiring uniform thickness, pressure-bubble plug-assist vacuum forming is a preferred method. In this thermoforming process, controlled air pressure is exerted against the heated sheet to create a bubble. Once the bubble reaches the correct height, a male plug-assist is lowered, forcing the bubble into the mold.
Trapped sheet contact pressure thermoforming uses both vacuum and air pressure to force the heated plastic into a mold. This process requires a lower temperature, is faster, and has a finer finish. Vacuum snap-back processing is a slower and slightly more complicated process that can be used when uniform thickness is more critical. In this method, the heated plastic sheet is placed over a vacuum box which sucks it down into a concave shape. The vacuum box then releases the plastic, and it snaps back against a male plug mold.
Billow and matched die are two methods of thermoforming which do not use a vacuum. In billow forming, the heated plastic is attached to a billow, a chamber which blows air, and the air pressure presses the plastic against a mold. Matched die forming is used to create parts with two halves which mate. The heated plastic sheet is clamped together between two molds, and no vacuum or air pressure is required.