Superplastic forming is a specialized metalworking process that allows sheets of metal alloys such as aluminum to be stretched to lengths over ten times that of conventional alloys without degrading the material properties of the metal. The process allows for the manufacture of complex metal parts, which eliminates the need for bolts and fasteners to attach individual metal parts together into a larger unit. Metal forming of this nature is most often used in the aerospace industry, but also has applications for performance sports equipment, as well as in the energy, defense, and medical sectors.
The science of metalworking that is used in superplastic forming is broken down into three deformation conditions: micrograin, transformation, and internal stress superplasticity. The most important method for metals involves micrograin superplasticity, where crystalline grain structures are 10 microns in size or smaller. The temperature of the metal must also be at roughly one-half the melting point of the metal alloy being formed and strain rates range between 0.001 to 0.0001. These conditions limit the types of alloys that will exhibit superplasticity to a small number.
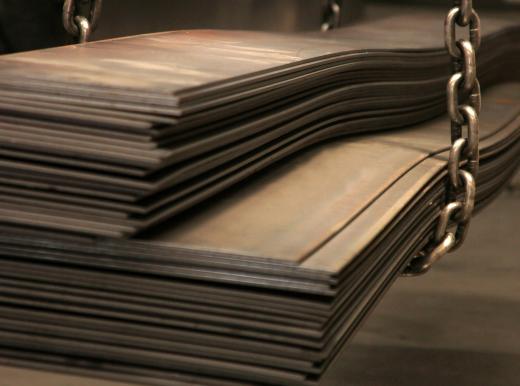
Industrial processes for sheet metal superplastic forming include vacuum and thermoforming, deep drawing, and diffusion bonding. Vacuum forming uses variation in gas pressures to shape metal into a die, while thermoforming uses established processes that are traditional to the manufacture of thermoplastics. Both methods are variations on hot metal gas forming, and have the advantage of requiring only a single die operation to create the part.
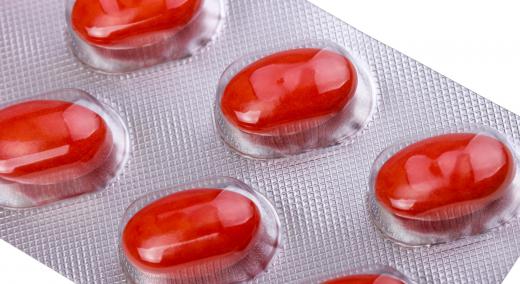
Deep drawing is a conventional method used in metal forming that can be adapted to superplastic forming. It requires strain hardening to achieve superplasticity. Thinning and rupture of the metal part, however, are possible in the process, so it is not usually a preferred choice.
Diffusion bonding was not initially a sheet metal forming process, but has been adapted to its use. Aluminum-magnesium alloys are commonly used with the method, and can have an elongation in the superplastic process of up to 600%, but usually don't exceed 300%. Parts created by superplastic forming and diffusion bonding are used in both automotive and aircraft applications that are not structural, and they are not as expensive as high strength alloys.
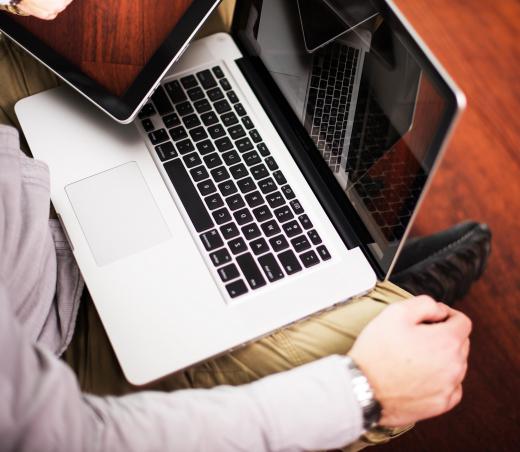
There are several advantages that metal sheet parts that have undergone superplastic forming have. Since their shapes can be more elaborate and larger due to the increased ability to stretch the metal, they reduce both the weight and cost of aircraft and automotive vehicles as well as metal parts in other industries. Assembly time and complexity is also reduced because fewer parts need to be fastened together. Stresses between multiple metal parts as they age and respond to temperature changes is also minimized.
The industry as a whole contributes to a wide variety of research and new products in the field. The increased versatility of metal sheeting shapes allows for innovation in new streamlining and designs in a multitude of industrial and consumer products. Superplastic forming is also key to innovation in aerodynamic and marine streamlining.