Plasma electrolytic oxidation (PEO) is one of several processes that coat the surface of a metal object with a protective ceramic layer. Materials that can be treated in this way include metals such as aluminum and magnesium, and the ceramic coating is typically an oxide. The process bears a resemblance to anodizing but uses substantially higher electric potentials, which can cause the formation of plasma discharges. This tends to create very high temperatures and pressures along the surface of a workpiece, which can result in somewhat thicker ceramic coatings than traditional anodizing is capable of. The protective layer created by plasma electrolytic oxidation can provide benefits such as resistance against corrosion and wear.
The first experiments with plasma electrolytic oxidation took place in the 1950s and various techniques have been developed and refined since then. Each of the PEO techniques works on the same basic principle, which is that certain metals can be induced to form a protective oxide coating under the correct conditions. Many metals will naturally form an oxide layer in the presence of oxygen, but it is usually not very thick. In order to increase the thickness of the oxide coating, anodizing and other techniques must be used.
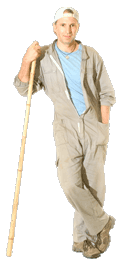
At the most basic level, plasma electrolytic oxidation bears a resemblance to traditional anodizing. The metal workpiece is lowered into an electrolyte bath and connected to a source of electricity. In most cases the metal workpiece will function as one electrode, while the vat that contains the electrolyte is the other. Electricity is applied to the electrodes, which causes hydrogen and oxygen to be released from the electrolytic solution. As the oxygen is released, it reacts with the metal and forms a layer of oxide.
Traditional anodizing uses around 15 to 20 volts to grow an oxide layer on a metal workpiece, while most plasma electrolytic oxidation techniques use pulses of 200 or more volts. This high voltage is able to overcome the dielectric strength of the oxide, which is what leads to the plasma reactions that the technique depends on. These plasma reactions can create temperatures of about 30,000°F (about 16,000°C), which is necessary for the formation of the thick oxide layers that PEO processes are capable of forming.
The oxide coatings that can be created through the plasma electrolytic oxidation process can be more than several hundred micrometers (0.0078 inches) in thickness. Anodizing can also be used to create oxide layers of up to about 150 micrometers (0.0069 inches) thick, though that process requires a strong acid solution as opposed to the dilute base electrolyte usually used for plasma electrolytic oxidation. The properties of a PEO coating can also be altered by adding various chemicals to the electrolyte or varying the timing of the voltage pulses.