OLE for process control is a set of standards pertaining to automated manufacturing process systems which facilitates industry-wide ease of communication between system controllers and plant equipment. The OLE identifier stands for Object Linking and Embedding, and the whole term is generally shortened to Object Linking and Embedding for Process Control, or OPC. The standards are of relevance to manufacturing processes based on the Microsoft Windows® Operating System (OS) and are governed by the OPC Foundation. OLE for process control was developed in 1996 in an attempt to create a standardized set of process communication protocols based on the Microsoft Corporation's OLE, DCOM, and COM technologies for their Windows® OS. The enforcement of the OLE for process control standards system allows ease of integration of automated manufacturing systems in a wide range of industries.
Automated manufacturing and industrial processes generally consist of three main sub-processes — flow planning, control, and floor systems. The processes are choreographed at the flow planning stage, while the control processes use the planning information to tell the floor systems what to do and when, and monitor the whole dance constantly to identify and rectify anomalies. This is, theoretically at least, a perfect system, but requires the control and floor systems to speak the same language at least. This is particularly true when new machinery or controllers are brought into the process.
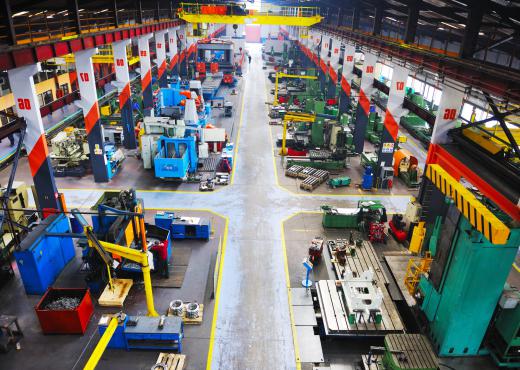
The OLE for process control system, or OPC, as it is more commonly known, has at its core a set of common objects, protocols, and interfaces. Together, these form a standardized communications bridge that ensures that control and execution systems can be moved about or added to a process seamlessly. As technologies in manufacturing and industry advance, so the OPC standards are upgraded and amended accordingly. The management of this process is handled by a group known as the OPC Foundation, which is responsible for its maintenance and implementation.
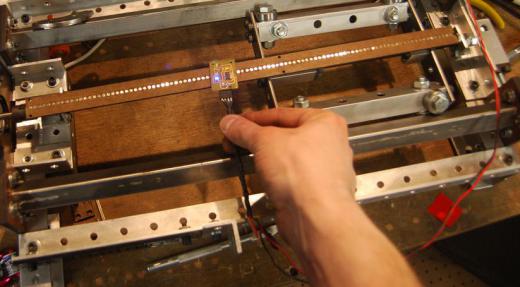
Prior to the advent of the OLE for process control system, a dedicated application had to be written for each new automated process. This was obviously time consuming and expensive, and created an environment where industry players and machinery manufacturers could not develop or implement common systems. This led to systems being developed in isolation with commensurate losses in streamlining and efficiency. The introduction of the OLE for process control standards can, thus, be seen as one of the most significant developments in the history of automated process control.