Metal Inert Gas (MIG) welding, also sometimes called Gas Metal Arc Welding (GMAW) is a process that was developed in the 1940s for welding aluminum and other non-ferrous metals. MIG welding is an automatic or semi-automatic process in which a wire connected to a source of direct current acts as an electrode to join two pieces of metal as it is continuously passed through a welding gun. A flow of an inert gas, originally argon, is also passed through the welding gun at the same time as the wire electrode. This inert gas acts as a shield, keeping airborne contaminants away from the weld zone.
The primary advantage of MIG welding is that it allows metal to be welded much more quickly than traditional "stick welding" techniques. This makes it ideal for welding softer metals such as aluminum. When this method was first developed, the cost of the inert gas made the process too expensive for welding steel. Over the years, the process has evolved, however, and semi-inert gases such as carbon dioxide can now be used to provide the shielding function, which now makes MIG welding cost-effective for welding steel.
Besides providing the capability to weld non-ferrous metals, MIG welding has other advantages:
- It produces long, continuous welds much faster than traditional welding methods.
- Since the shielding gas protects the welding arc, this type of welding produces a clean weld with very little splatter.
- It can be used with a wide variety of metals and alloys.
The primary disadvantages of MIG welding include the following:
- The equipment is quite complex, as MIG welding requires a source of direct current, a constant source and flow of gas, as well as the continuously moving wire electrode. Plus, electrodes are available in a wide range of sizes and are made from a number of metal types to match the welding application.
- The actual technique used is different from traditional welding practices, so there is learning curve associated with MIG welding, even for experienced welders. For example, MIG welders may need to push the welding puddle away from them and along the seam.
- The necessity for the inert gas shield means that MIG welding cannot be used in an open area where the wind would blow away the gas shield, unless other precautions are taken to prevent this.
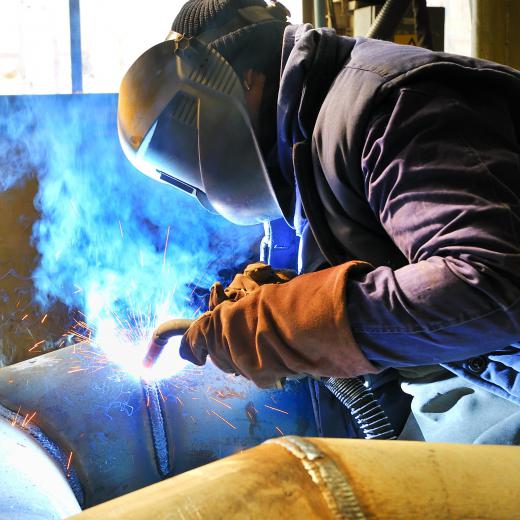
Since its development in the middle of the 20th century, MIG welding has become commonplace in many manufacturing operations. For example, it is commonly used in the automobile industry because of its ability to produce clean welds, and the fact that it welds metals quickly.