Laser cutting aluminum can be more difficult than using lasers for precision cutting of carbon steel, stainless steel or other materials. Aluminum is difficult to cut with a laser because it is both reflective and has a high thermal conductivity, the ability to shed heat. Because of these characteristics, laser cutting aluminum requires special handling and equipment to provide adequate quality of the aluminum.
There are two major classes of lasers used for metal cutting. These include neodymium or neodymium-doped crystal lasers, and carbon dioxide (CO2) gas lasers. Crystal lasers focus and amplify the light beam through a solid crystal composed of the elements that describe them. CO2 lasers use carbon dioxide gas to manage the laser light beam.
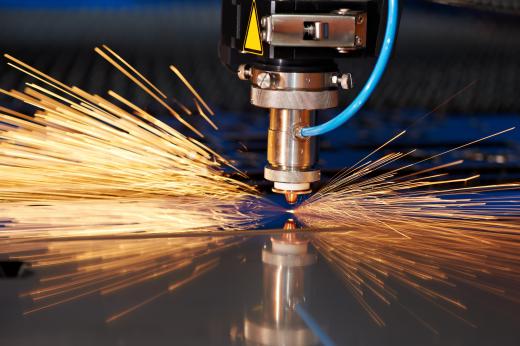
In addition to the laser, gas-assistance technology may be employed. Gas-assist systems use a stream of gas either passed through the laser beam nozzle or through a secondary nozzle. This removes melted metal, gases and other materials away from the cutting zone.
To cut aluminum with a laser requires higher powered lasers than may be required for other metals. Gas-assist is often needed to prevent molten slag from accumulating at the bottom edge of the cut. Aluminum conducts heat and cools quickly, which can result in a poor finish cut. Thicker aluminum sheet will normally require the use of a CO2 laser, which is more powerful than the neodymium-class lasers.
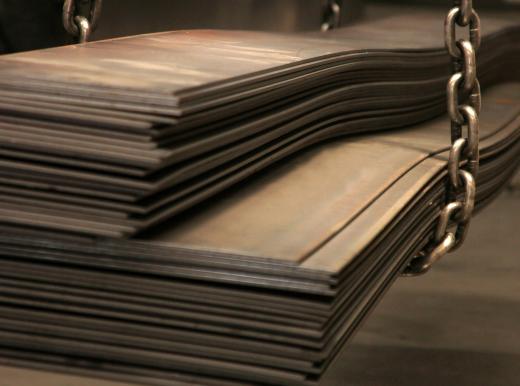
Laser cutting aluminum can be accomplished by either moving the aluminum sheet beneath the optical cutting head, or by moving the optical head over a stationary sheet of aluminum. The latter method is referred to as a flying optics system, and is usually connected to a computerized cutting system. Flying optics systems are more common for large industrial cutting operations, because the size of the aluminum sheet stock can be very large and would be difficult to move under a stationary cutting head.
There are a number of considerations to be made when laser cutting aluminum. Electrical power consumption can be significantly higher during this process than for other cutting technologies. Consumption of power can also be significantly higher than what is required for other metals. Additional costs are incurred by the need for gas-assist to remove waste material and maintain high cut quality.
The high thermal conductivity of aluminum may limit the thickness of aluminum that can be reasonably cut with laser systems. Laser cutting aluminum creates high cut edge temperatures that can change the metal properties in the vicinity of the cut, which may require additional heat treating. Understanding these considerations is key to the cost-effectiveness of the process.