Inert gases, or noble gases, are the gaseous elements in the helium group of the periodic table which are considered chemically nonreactive. These gases, which do not form chemical compounds, are helium, neon, argon, krypton, xenon and radon. Inert gas welding is a welding process which uses an inert gas to protect the weld during the welding process.
During the welding process, an electric arc is struck between the electrode on the welding equipment and the work piece. This arc creates heat which fuses the edges of the metal pieces being joined, as well as any consumable electrode being used, forming the weld joint. The gases used in inert gas welding include argon, helium, carbon dioxide or a combination of gases like argon and oxygen.
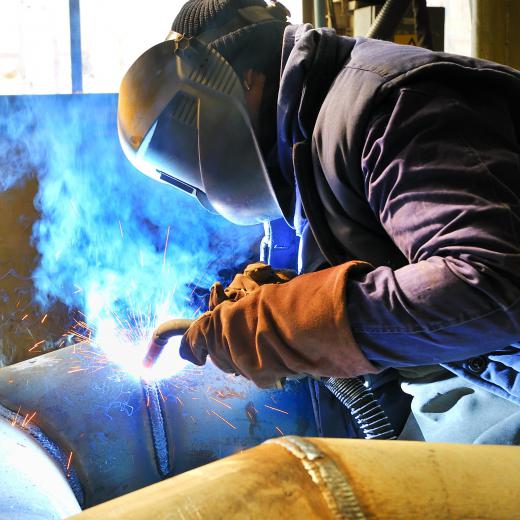
Metal inert gas welding (MIG)uses a consumable electrode, or solid electrical conductor, made of a filler metal wire. An electric arc forms between the electrode and sheet metal being welded. An inert gas surrounds the weld protecting it from oxidation. This method works with carbon steels, low alloy steels, stainless steels and most aluminum, copper and zinc alloys. MIG welding can be used to weld metals with thicknesses ranging from two-tenths to one-quarter inch (.5 mm to 6.3 mm).
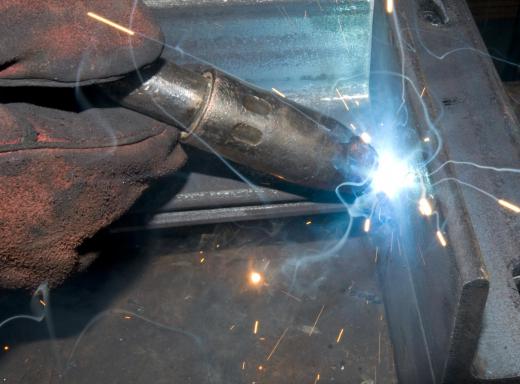
Tungsten inert gas welding (TIG) uses a non-consumable electrode made from tungsten. Unlike MIG welding, tungsten welding does not require a filler material. This method can be used on the same metals as MIG welding, but it does a better job of welding dissimilar metals together. One advantage of TIG welding is that it can join pieces as thin as five-hundredths of an inch (.125 mm).
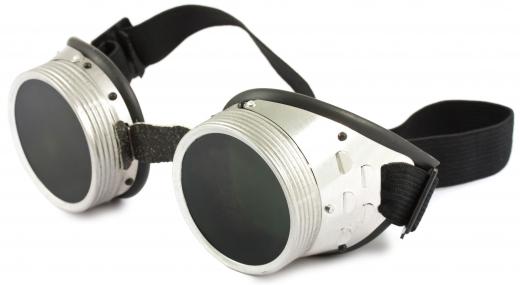
The location and cosmetic importance of the weld will help determine which form of inert gas welding to use for a particular application. MIG welding is less expensive and does not require a high level of expertise from the operator. The weld is messier, however, because of the use of the consumable electrode, or filler material. If the weld is in an area which is visible, MIG welding is generally not recommended because it causes a lot of spatter which needs to be sanded or filled.
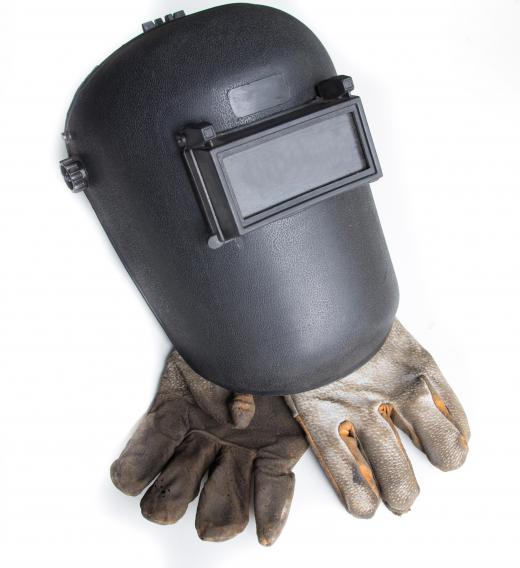
TIG welding is a bit more expensive than MIG welding, but is the recommended method if appearance is important. There is no spatter created during the weld because the non-consumable tungsten electrode does not use any filler material. This method does require a higher level of operator training and expertise. Argon is the most commonly used gas for TIG welding.
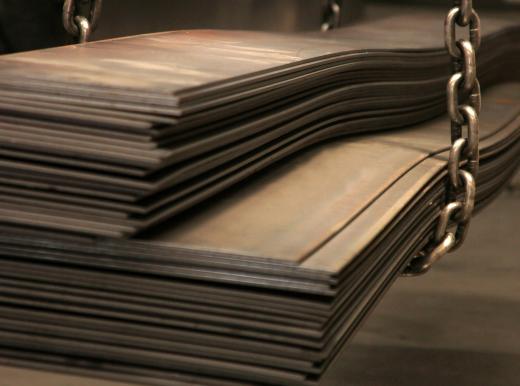
Inert gas welding has been used since the 1940’s, and is faster than traditional welding methods. It can produce cleaner, longer continuous welds, especially with thinner materials. One drawback of this form of welding is that the equipment is less portable and more expensive than other gas welders. Another limitation is that inert gas welding must be done inside and not in an open area where the wind can interfere with the protective gas shield.