Direct reduced iron (DRI) is a type of alternative iron made by heating iron ore so that the oxygen and carbon burns off while the temperature is kept below iron's melting point. Direct-reduced iron is also known as sponge iron and is sold as briquettes, lumps, or pellets. It is typically used in smaller scale steel mills to enhance the condition of the steel that is manufactured.
During the reduction process in the production of direct reduced iron, either coal or a special gas — commonly containing a combination of carbon monoxide and hydrogen — is used. This mixture functions as a reducing agent and facilitates the decrease in the iron's oxygen and carbon content. The result is a type of iron that is 90-97% pure, containing only minuscule amounts of carbon and other impurities.
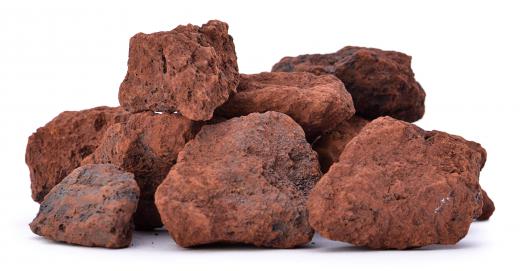
DRI was the most prevalent form of iron production throughout Europe and the Middle East until the 16th century. The introduction of the blast furnace helped revolutionize the iron manufacturing process and soon became the standard for production. As demand for iron increased, the blast furnace made it possible to produce large amounts of iron in a relatively short period of time. The type of iron made by blast furnaces, however, is not direct-reduced iron but pig iron, which isn't as rich as direct reduced iron.
In the modern era, direct reduced iron is considered an alternative method of making iron. The process of crafting iron via the direct-reduction route has a distinct advantage over the more traditional, blast furnace mode of production. Not only is the resulting iron more plentiful in total iron content, but it entails a much cheaper production process than the operation of a large blast furnace.
There are also significant drawbacks to DRI. The manufacturing procedure requires unusually large quantities of natural gases, which limits the areas of the world in which it can be produced. India, a nation rich in the necessary supplies of natural resources, manufactures more direct reduced iron than any other country. Other locations where natural resources are not so abundant utilize different variations of the traditional manufacturing process.
Another disadvantage to direct reduced iron is its sensitivity to oxidation and rusting. It needs to be stored and used in temperature-appropriate conditions to ensure its longevity. DRI in large amounts has also been known to spontaneously burst into flames when exposed to open air.