Die casting is a process in which various metals can be cast from molten states into a mold. These molds are called "dies" in many foundry environments. The die is filled with typically non-ferrous metals, such as zinc and aluminum. It is filled in a high-pressure application that ensures that the density of the die-cast material is at the desired level.
The metal is injected into a specific cavity or mold that has been created. This is then machined to create two opposing steel dies. After the cooling process is completed, the casting is then removed from the mold. It is next burred or buffed to create a product that has been manufactured to exact specifications.
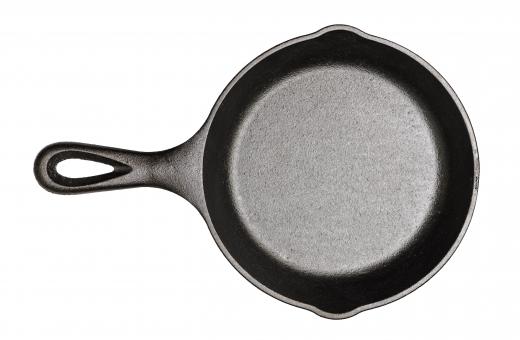
The process of die casting has evolved since its original inception to become much more efficient, in terms of both production and a decrease in the creation of scrap materials. When the molten metal is injected into the mold, this shot uses between 1,500 pounds (680.39 kilograms) to over 25,000 pounds (11,339.08 kilograms) per square inch of pressure. This is to ensure that the entire mold is filled with material to create consistent and full mold shots. The term shot refers to each mold being injected, since there can be multiple molds within a mold casing, and multiple castings produced within a shot.
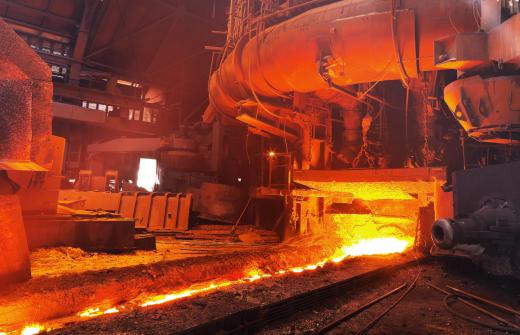
Die casting has long been a valuable means of producing hardened metal products, such as engines. Many other items are also cast into molds from molten states, such as cast-iron pots and pans, and other car parts. This method of production has been used in industrial settings to create a multitude of different products, mainly because the casting process is able to produce parts of virtually any size and shape, depending on the mold that has been created for the metal to be poured or injected into.
Virtually any part that is needed for a specific application can be cast from almost any metal. One of the most popular, however, is aluminum. The low melting point and the ease of machining applications with aluminum make it an easily manipulated material to work with. This, in turn, results in a lower cost of production.
Due to the increased initial cost for the die casting equipment and the facilitation of a die casting operation, most of the industrial environments that have these types of productions take place do so on a large or heavy production scale. This is especially true in the automotive industry. There, the bulk of many automobile engines are made out of cast metal parts.