Splicing is a method of rejoining a broken conveyor belt, whether the break is new or an already spliced belt has been damaged or come undone. Broken conveyor belts in production environments in manufacturing, on construction sites, or in mining operations can lead to considerable downtime for workers dependent on their output and the reduced production and financial losses can mount quickly. There are many types of conveyor belts in operation and they are made of diverse materials; thus, splicing techniques are designed to create splices quickly that last as well as preserve the integrity of the conveyor belt. Many belts can be repaired by means of one particular splicing technique only, one recommended by the manufacturer and using only manufacturer-provided materials.
A conveyor belt splicing method called mechanical splicing, making use of several types of metal fasteners, is a quick and versatile method in use in dirty and confined environments such as mining operations. These fasteners splice belts using rows of connecting grips and are preferred for in-the-field conveyor belt repair. They’re relatively inexpensive, appropriate for holes and tears, and require only basic mechanical aptitude and skill to use in conveyor belt splicing. As the fasteners are hinged and separable, they can quickly be removed and replaced without having to remove the belt from its support system, which can cut the splicing task time considerably.
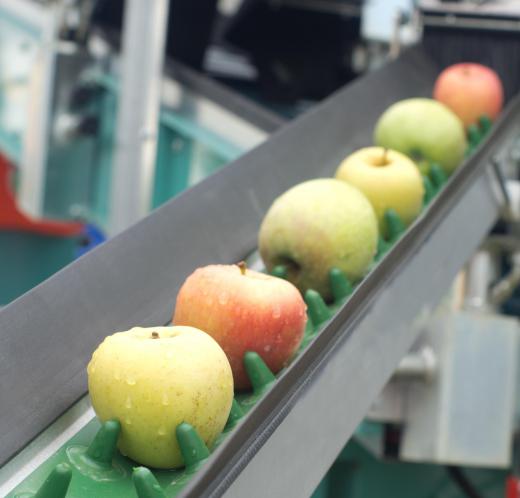
Conveyor belts come in single or multiple ply strengths, and the thickness of the ply as well as the diameter of the pulleys will dictate which fastener type to use for conveyor belt splicing. Regardless of type, starting with a straight edge that is squared on the end and being careful not to bury the fasteners too deep can help keep the spliced edges from becoming damaged or causing too much wear on the hinge-pins. As the fasteners may need to be replaced at a later date, good installation practices will preclude tracking problems and help to avoid further downtime and possible employee injuries and equipment damages.
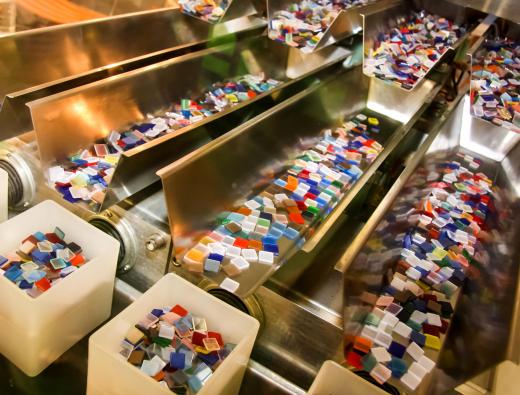
Some thermoplastic belts cannot use metal fasteners, but instead are attached using plastic rivets. These rivets are installed using a portable machine that spin-sets them. There are also plastic spirals in a webbed material that are vulcanized to the ends to splice conveyor belts. Craftsmen skilled and experienced in vulcanization techniques must install these.
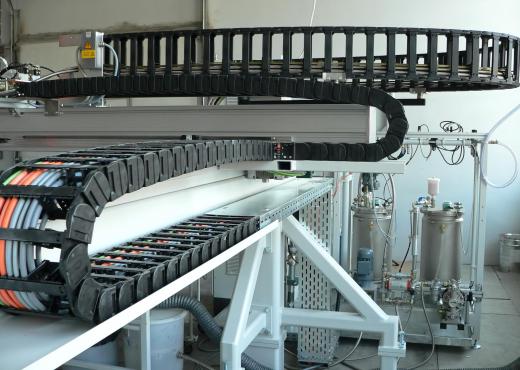
Some conveyor belts must be spliced using hot vulcanization, using heated presses, or cold vulcanization, using chemicals to bond the materials in a seamless repair. Good conveyor belt splicing technique in vulcanization or when fusing thermoplastic splices requires special conditions such as a clean, dust-free, temperature- and humidity-controlled environment. Conveyor belt splicing technicians in such cases are engineers, experienced in the techniques to effect conveyor belt repairs according to the specifications of the manufacturer, using only manufacturer-provided materials.
Vulcanization delivers a splice that is leak-proof, with absolutely no interference or friction at the splice to wear on the support system, and though it is a more costly repair, this conveyor belt splicing will typically last far longer. Another type of conveyor belt splicing recommended by a manufacturer and installed by manufacturer-trained employees are the preform splicing mat techniques performed on certain steel conveyor belts. Preform splicing is more cost-efficient and has been tested to be as much as 11 percent stronger than typical vulcanized splices and between 16 and 25 percent faster than typical vulcanization procedures.