The term "acrylic" is used for products that contain a substance derived from acrylic acid or a related compound. Most often, it is used to describe a clear, glass-like plastic known as poly(methyl) methacrylate (PMMA). PMMA, also called acrylic glass, has properties that make it a better choice for many products that might otherwise be made of glass. There are two basic types: extruded and cast.
Types
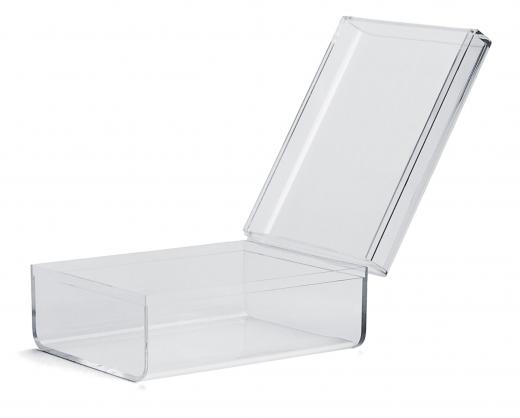
Extruded acrylic is made through a process in which the liquid plastic is pushed through rollers, which press it into sheets as it cools. This is a comparatively inexpensive process, but the resulting sheets are softer than cast acrylic, can scratch easier, and may contain impurities. Extruded acrylic is still generally considered to be good quality, and is usually the more common type made available on the market.
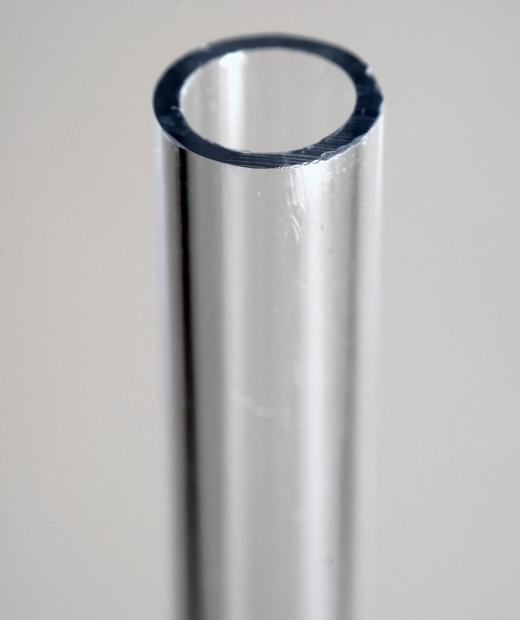
Cell cast acrylic tends of be of higher quality than extruded, but it's also more expensive. In cell casting, single sheets are made by pressing the liquid plastic between pieces of a mold, often made of glass, which is then taken through a gradual heating process. The resulting sheet is stronger than extruded acrylic. This type is often used for aquariums, awards, and other products that require shaping or machining of the final product.
Advantages
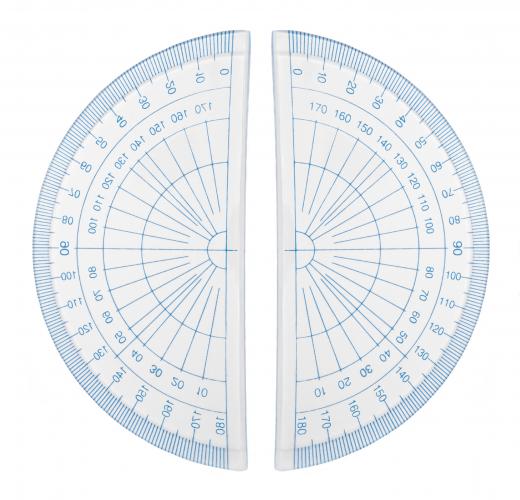
Many different products are made from acrylic, including shower doors, bath enclosures, windows, and skylights. It is many times stronger than glass, making it much more impact resistant and therefore safer. Falling against a shower door will not likely break it, for example; baseballs that would otherwise crash through glass windows will, in most cases, just bounce off acrylic windows. It also insulates better than glass, potentially saving on heating bills.
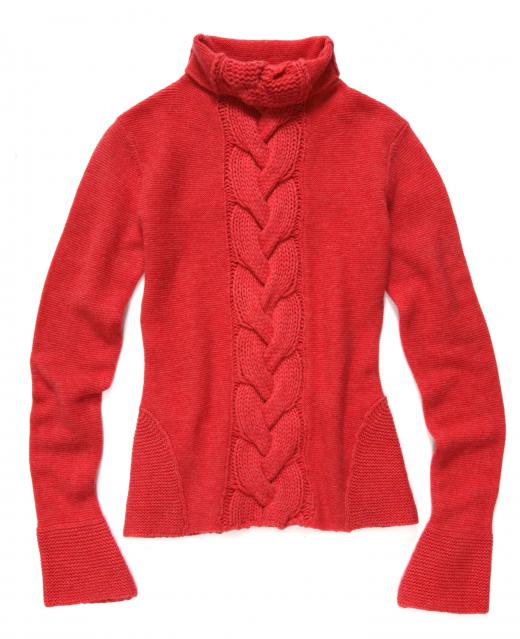
Acrylic glass is also very clear, allowing 92% of visible light to pass through it. Very thick glass will have a green tint, while acrylic remains clear. It also weathers well, keeping its clarity over the years without turning yellow or breaking down when exposed to sunlight over a long period of time.
Another advantage of acrylic is that it is only half as heavy as glass. This makes this material easier to work with, and makes it a better choice for projects where weight is an issue. It can also be sawed, whereas glass must be scored.
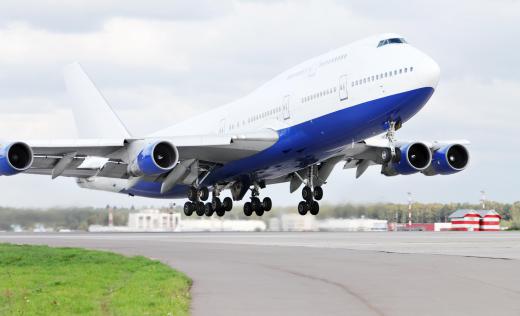
Virtually all major public aquariums now build display tanks out of this thermoplastic, and it is often used in many other buildings. When this material is just over 1 inch thick (about 25 mm), it is bullet resistant; the presidential motorcade, the pope's booth-vehicle, teller enclosures, and drive-through window enclosures all feature bullet-resistant acrylic. It is used for airplane windows as well.
Shaping
A unique property of this thermoplastic is its ability to be shaped. Extruded acrylic is not as strong as cell cast, and tends to crack or splinter when being machined, so most higher quality products are made from cast acrylic. Structures can also be made with no seams, as chemical welding at the molecular level actually "melts" seams into one piece of solid material. Seams that are welded and polished correctly are invisible.
Misconceptions and Disadvantages
There are some misconceptions about acrylic, namely that it yellows, turns brittle, and cracks over time. Though this might be true of cheap forms of plastic, it is not so with acrylic. If taken care of, this material can remain new looking for several decades, regardless of age or exposure to sun. Some people worry that it scratches too easily, but unlike glass, scratches may be buffed out.
For all of its advantages, there are two disadvantages of acrylic: It is more expensive than glass, and if exposed to a direct flame, it will melt and eventually burn. Burning releases toxic fumes, so safety precautions should always be taken when it is being cut with power tools or bent using heat. When it is not cared for properly, or when inferior acrylic is used, it can scratch, and improperly made joints can be very visible.