A rotary furnace, also called a rotary kiln, is a long tube that is used as a continuous plug flow reactor in the mineral industry. The mineral feed is introduced to the reactor portion and is transported down the length of the tube while the tube slowly rotates around its central axis. The materials are mixed as well as heated. The original designs were applied to the calcination treatment in the production of Portland cement and in the extraction of mercury from ores. These reactors are used frequently for the recovery of valuable metals.
A typical rotary furnace is made from a single sheet of steel wrapped into a cylinder with a diameter of about 3 ft to 6 ft (0.9 m to 1.8 m) and a length of about 30 ft to 60 ft (9.1 m to 18.3 m). In one common drive configuration, the tube is rolled on smooth stainless steel rings that rest on two stainless steel rotating rollers. Usually, there are multiple heat zones. The heat may be applied via the hot gas discharge from the fuel, or the fuel may be fired directly into the tube. The transformed product is discharged after being cooled in a cooling section where heat is recovered and sent back to the combustion air.
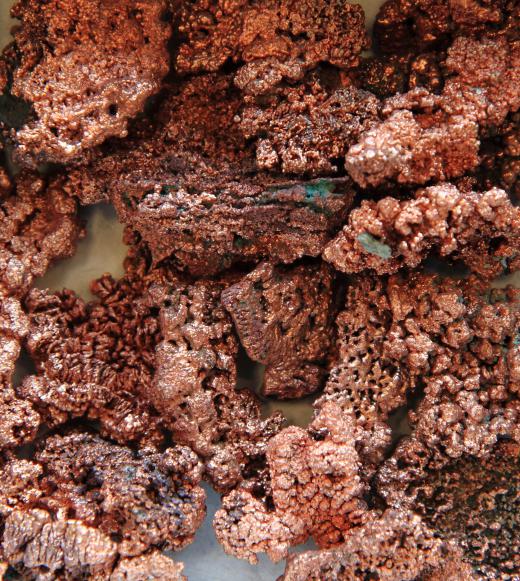
Screw conveyors or simple threaded rods can be used in a separate rotary furnace design in which more mixing is desired. Another configuration consists of a reverberating design in which material is shaken down the tube. The rotary furnace design is modified by a tilt mechanism that allows liquid metal to drain from the reactor. This design is very useful in the extraction of metals from ores or from recycled materials, such as copper, gold, and mercury.
Fuel is limited to high-energy content fuels, such as oil, gas, or fluidized coal since high temperatures are required. The high-energy requirement to melt metals also explains the use of direct contact with the combustion flame in some designs. The combustion gases are generally passed counter-current to the material flow. Controls include feed rates, temperature zones, and rotation speeds. Many companies now provide complete systems that are either of standard design or custom engineered for the applications.
A variation of the rotary furnace is a batch process that consists of a rotating vessel that is titled on its side. The heat is supplied through the free space above the liquid. When the metal is melted, the vessel is tilted, and the metal is poured into molds. This is a common design for the recycling of aluminum cans, as the cans are primarily aluminum and organic materials that can be burned off during the melting process.