A melting crucible is usually a pot-shaped container placed in the center of a furnace that is used to hold a metal to be melted. It is commonly made of silicon carbide and graphite, but can also be composed of metals suited to high temperature applications, such as tantalum or tungsten. Crucibles can also be shaped in a conical or planar, plate-like form, depending on the application.
The industrial crucible is one of the oldest and simplest designs in the metallurgy industry. Foundries typically use them to melt smaller amounts of metal or specialty alloys than larger, commercial foundries process. Methods for heating the furnace that contains one of the various types of crucibles can be anything from natural gas or propane firing to the use of oil, coke, or induction electricity.
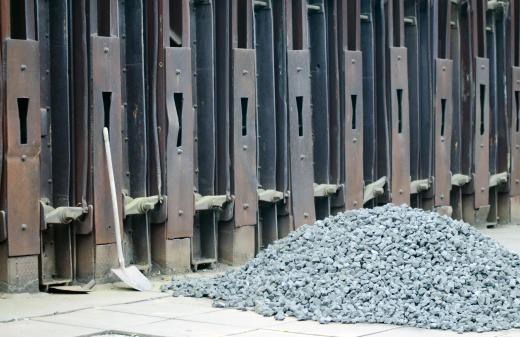
The melting crucible shapes are referred to as a bilge for the cylindrical shape and an A-shape for conical shapes, with A crucibles being less expensive as they are easier to manufacture. The material from which the melting crucible is made also determines what temperature level it can withstand. A silicon carbide crucible can withstand temperatures up to 2,750° Fahrenheit (1,510° Celsius). This makes them suitable for handling all soft metals such as gold, silver, and aluminum, as well as alloys such as brass, which is mostly composed of zinc and copper.
Iron and iron alloys are not typically processed using a melting crucible furnace, as the melting point of iron is very high. A standard silicon carbide crucible structure would break down and contaminate the metal sample, since iron melts at 2,800° Fahrenheit (1,538° Celsius). A crucible with a graphite mixture, such as silicon carbide models have, is also not used for iron melting as the graphite dissolves in and reacts with the iron, altering its content and slowly wearing away at the crucible structure. Specialized crucibles made of molybdenum metal can withstand very high temperatures, however, of 4,712° Fahrenheit (2,600° Celsius) and may be used to melt iron.
Furnace designs that use a melting crucible are labeled by the way in which the molten metal is removed from the crucible. A bale-out furnace has a crucible where molten metal is ladled out of it, while a tilting furnace has a crucible that is tilted to pour out the metal. Lift-out furnaces are designed so that the entire crucible structure can be removed and the molten metal ladled or poured out.
Aluminum compositions are common to crucibles as well, as they can be inert under a wide array of metal chemistries. They work best, however, with a neutral acid level for the melt materials. Magnesite crucibles are better suited to basic melt compounds and zircon-silica crucibles to highly acidic compounds.
Crucibles also undergo stress when repeatedly heated and cooled. This is known as thermal shock, and some metal compounds for the crucible walls handle this better than others. The temperatures being applied, chemical compositions of what is being melted, and the amount of prolonged use a melting crucible will experience are all important factors to consider in choosing a model that is best suited to the foundry's needs.