A linear encoder is a type of electronic sensor that is able to measure a position along a straight line. They are commonly used in robotics and automation systems. There are several different types of linear encoders, each using a different detection method to determine the encoder location.
All varieties of this instrument require both a scale and a sensor to use properly. The scale is a straight piece of material that is marked at consistent intervals, similar to a common yardstick. A sensor within the linear encoder device is able to detect each of these intervals as it moves past the slide. Each time an interval marking is detected and counted by the sensor, the output of the linear encoder changes.
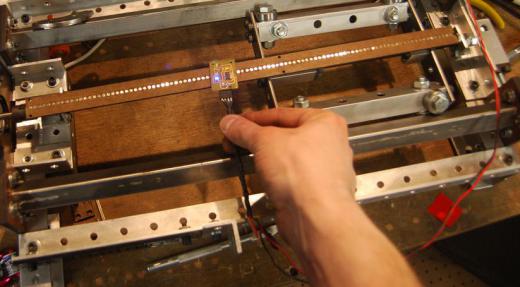
Optical linear encoders are very common, and use high contrast visible markings on the scale. The sensor on this instrument usually emits infrared, visible, or laser light onto the markings. Light pulses reflected by the scale markings are detected and counted. An optical encoder can be very accurate, and is often able to determine linear position within one micrometer.
Not all linear encoder markings are visible to the human eye. Magnetic encoders use small magnetic areas embedded onto the scale. Each area of magnetism is detected by the sensor and counted. These are usually not quite as precise as the optical variety, but can be used in dirty or humid environments that would impede optical detection methods.
A third type of encoder uses eddy current to determine position. Eddy currents are created by the movement of a magnetic field past a conductor. The scale of an eddy current encoder is designed to have different levels of magnetic resistance. Areas of low and high magnetic resistance are detected by monitoring the eddy currents caused by induction.
Position data detected by a linear encoder can be either incremental or absolute. Incremental position readings simply indicate how far the encoder has moved in a straight line. Absolute readings, on the other hand, contain data about precisely where the encoder is located along the scale.
Linear encoder data is sometimes only used for informational purposes on a readout or display. The data can also be used as part of a more sophisticated computer controlled system. Encoders are often used to provide a computerized device, such as an industrial robot or automated machine, with feedback on the location and travel distance of moving parts.