A gear hobber is a machine that manufacturers gears, in addition to similar parts such as sprockets and splines. It uses a cutting tool, or hob, to make teeth in the work piece with a series of progressive cuts. This process is accurate and relatively inexpensive, making it the most common method of cutting gears. A gear hobber is suitable for making gears in a wide range of quantities and styles.
A pair of spindles are used with a gear hobber. The hob is mounted on one spindle, and the work piece is mounted on the other spindle. The angle between these spindles depends on the specific type of gear that the gear hobber is making. The gear hobber then rotates the shafts of the two spindles, which causes the hob to begin cutting the work piece.
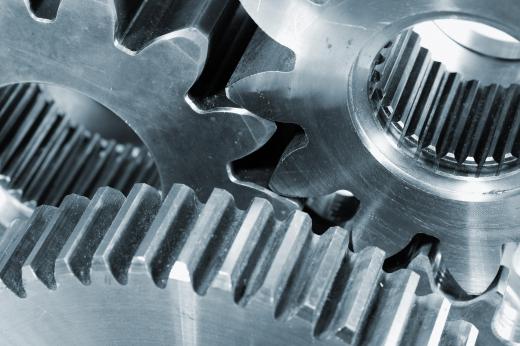
The ratio of the rotation speeds between the two spindles determines the number of teeth that the hob cuts into the work piece. The number of teeth that the gear will have is equal to the number of threads in the hob multiplied by the gear ratio. For example, if a hob with two threads rotates 10 times more quickly than the work piece, the hob will cut 20 teeth into the work piece. A large work piece might already have rough cuts before it is mounted onto the hobber. This allows the hobber to make the final cuts more easily.
Gear hobbers are classified according to the largest gear that it can produce. For example, a hobber that can make a gear with a 12-inch (30.5-cm) pitch diameter is known as a 12-inch (30.5-cm) hobber. A modern gear hobber might be capable of producing gears up to 10 feet (3.05 meters) in diameter. Gear hobbers have drive motors, and larger hobbers typically have a tail stock and chuck.
A vertical hobber mounts the work piece vertically, and a horizontal hobber mounts the work piece horizontally. Vertical hobbers are generally the most common, although horizontal hobbers are more useful for longer work pieces. For example, a spline at the end of a shaft will probably require a horizontal hobber.
The hob for a gear hobber is cylindrical with cutting teeth arranged in a spiral pattern. These teeth contain grooves that help cut the work piece and remove chips from the work piece. Hobs typically have one thread, although they might have two or three threads. Multi-threaded hobs are faster but less accurate.