A compressor blade is a blade machined to a precise and exacting standard to be used for application inside a turbine or compressor engine. The blades are the driving force to move air to the compression unit. The air is then forced into the tank for a compressor unit.
Applications that involve industrial turbine motors often use a compressor blade as the main component of the air or gas moving process. Compressor blades must be machined with a great deal of precision. The compressor blade must move as much air as possible with as little motor drive as possible to make the operation efficient.
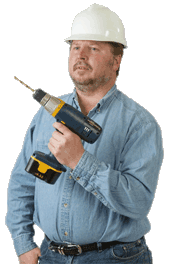
The materials that compressor blades are typically made out of are lightweight, yet strong. A compressor blade is generally made using an alloyed metal that is able to be machined to a precision angle and dimension. Sometimes, the blades are machined out of aluminum because of the material’s weight and ease of shaping.
A compressor blade can also be made out of more expensive materials. This is appropriate depending on the specific application in which it will be used. A stronger and more lightweight material allows for a more stable and constant movement of as much air as possible without the blades suffering any material instability.
Compressor blades are always manufactured with a connection method that allows them to be applied to the motor wheel as securely as possible. This means there is as much surface contact between the motor wheel and the blade base as possible. This is to help ensure that the connection between the blade and the motor wheel doesn’t allow for shaking or shifting.
Shaking or shifting could alter the draw and push of the blade in its function. This would be highly detrimental to the function of a compressor or turbine engine. Both of these types of engines require the utmost amount of balance in their movement.
There are different shapes in which the compressor blades themselves can be formed and machined. Typically, they are made in specific geometric shapes according to the specific task that the turbine or the compressor is required to carry out. Due to the fact that some turbines are required to move extremely measured amounts of air, the blades require specific machining to both pull and deliver the prescribed amount of air. As a result, most blade manufacturers have begun testing newer, more innovative methods of producing these blades, including multi-axis grinding applications.