There are dozens of different methods for thin film silicon deposition, but they can generally be broken down into three categories. There are chemical reaction deposition processes, such as chemical vapor deposition, molecular-beam epitaxy, and electrodeposition. Physical vapor deposition is a deposition process where a physical reaction alone takes place. There are also hybrid processes that use both physical and chemical means, which include sputter deposition and gas or glow discharge methods.
Physical vapor deposition is related to the variety of sputtering technologies used, and involves evaporating material from a source and transferring it in thin film silicon layers to a target substrate. The source material is evaporated in a vacuum chamber, causing particles to equally disperse and coat all surfaces in the chamber. The two methods physical vapor deposition use for this are electron beams, or e-beams, to heat and evaporate the source material, or resistive evaporation using high electrical current. Sputter deposition uses a partial vacuum loaded with an inert yet ionized gas, such as argon, and the charged ions are attracted to the target materials used, which break off atoms that then settle onto the substrate as thin film silicon. There are many different types of sputtering, including reactive ion, magnetron, and cluster beam sputtering, which are all variations on how ion bombardment of the source material is done.
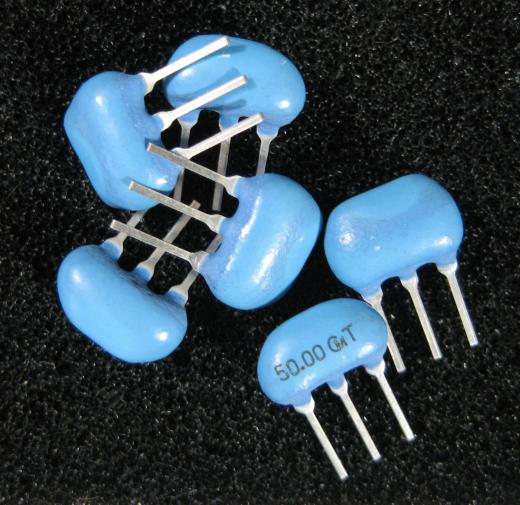
Chemical vapor deposition is one of the most common processes used to produce thin film silicon, and is more precise than physical methods. A reactor is filled with a variety of gasses, which interact with each other to produce solid byproducts that condense on all surfaces in the reactor. Thin film silicon produced in this manner can have extremely uniform characteristics and very high purity, which makes this method useful for the semiconductor industry as well as in producing optical coatings. The drawback is that these types of deposition methods can be relatively slow, often require reactor chambers operating at temperatures up to 2,012° Fahrenheit (1,100° Celsius), and utilize very toxic gasses, such as silane.
Each of the dozens of different deposition processes must be considered when manufacturing thin film silicon, as each has its own unique advantages, costs, and risks involved. Early reactive ion chambers were suspended from the lab floor to isolate them, as they had to be charged to 50,000 volts and could short out computer equipment even if they were merely sitting on concrete nearby. Twelve-inch diameter copper pipes that ran from these reactors into the bedrock below the manufacturing floor, were colloquially known as "Jesus sticks" by the lab workers, with reference to the fact that whoever touched it would be talking to Jesus since it would kill him or her. Products like dye-sensitized solar cells offer a new, less dangerous, and less expensive approach to thin film manufacturing, as they don't require precise silicon semiconductor substrates, and can be produced at much lower temperatures of around 248° Fahrenheit (120° Celsius).